Principle Components and Information
The MAT-SIM facility includes (Figure 1 and Figure 2):
- Two Linear (ShoreWestern) Actuators capable of imposing any displacement and/or force on structural components. The force and stroke capacities of the actuators are +/- 24 kips and +/- 10 inches. The tests conducted by these actuators could be displacement control, force control or mixed (displacement and force) mode control.
- One dynamic actuator5.5 kip (25 kN) fatigue rated, oversized non-metallic bearings, one-piece, double ended 1¾ inch (44.4 mm) alloy piston rod, and concentrically mounted internal LVDT. Trunnion and swivel dual mounting.
- Strong reaction frame: The facility is equipped with a strong reaction steel frame which enables testing of full-scale sub-structures. The frame can handle high static and dynamic forces with minimal/negligible deformations. The actuators are mounted to the strong frame (as shown in Figure 2) at one end and to the tested specimen at the other end. The strong reaction frame provides almost infinite stiffness and strength and enables testing of stiff specimens of high force capacities.
- An 11 gpm (ShoreWestern) pump: the pump provides actuators with oil to impose force and/or displacement.
- ShoreWestern Controller: the controller controls the flow of oil from the pump to the actuator to achieve the targeted displacement and/or forces during the test. The controller software is capable of imposing static as well as dynamic target forces/displacements to the tested specimen with very high precision.
- Data acquisition system (DAQ): include advanced measurement systems of strains, displacements and slippage at critical locations of the specimen. The DAQ consists of the software (from National Instruments) which is capable of not only recording the test data but also post-process the data and provide results in different formats. The software can handle up to 80 channels. DAQ also includes strain gauges, potentiometers, LVDTS and load cells. Data Acquisition system also includes high resolution cameras and image processing software capable to capture deformation on the micro-scale of the tested structural component.
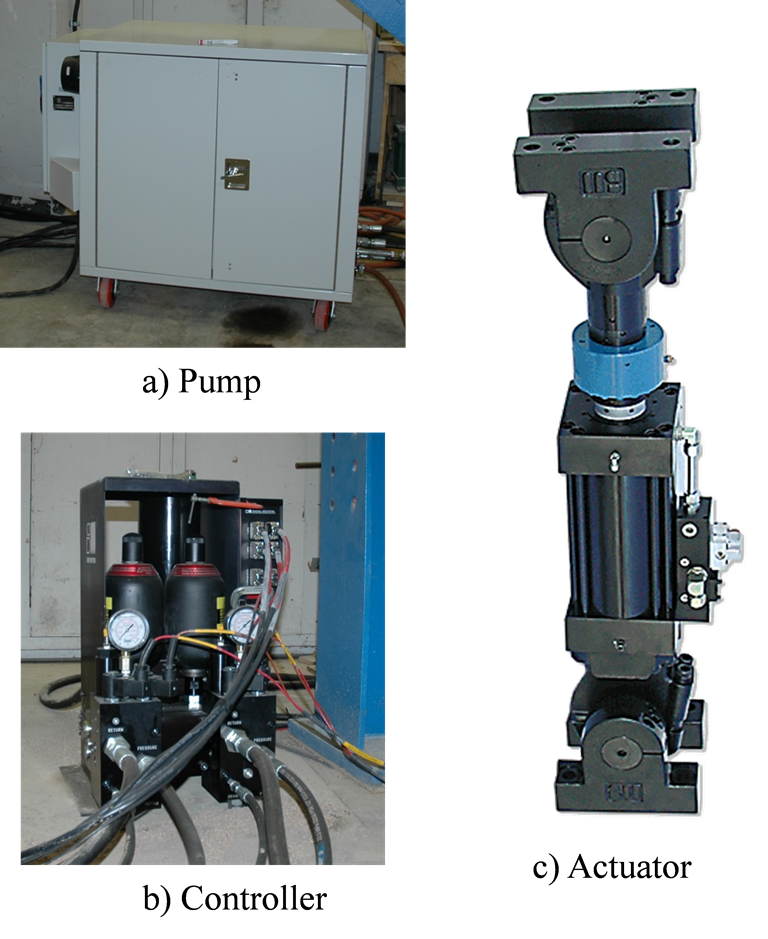
Figure 1: Pump, controller and actuator.
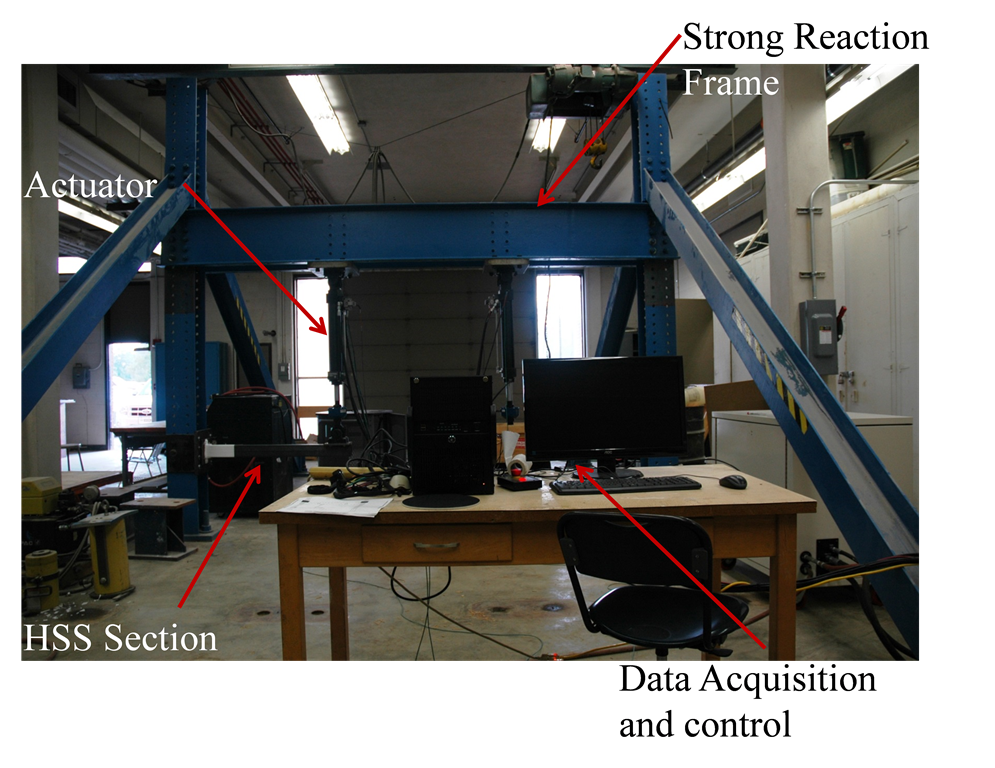
Figure 2: Strong frame, actuators and data acquisition and control system (MAT-SIM Facility ES BLDG Room 109).
top |
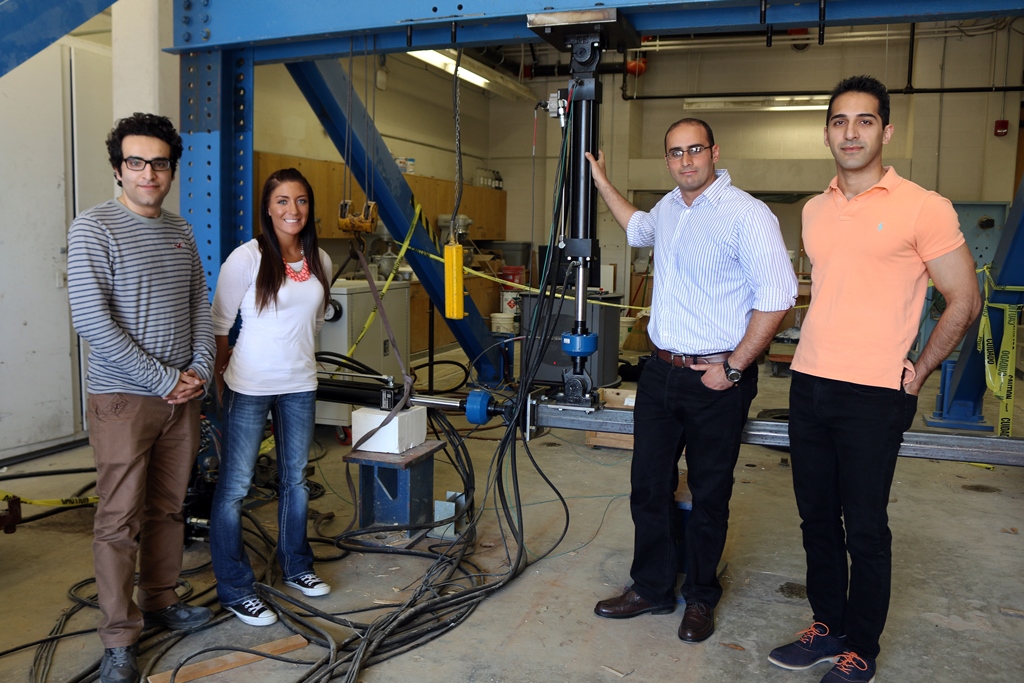
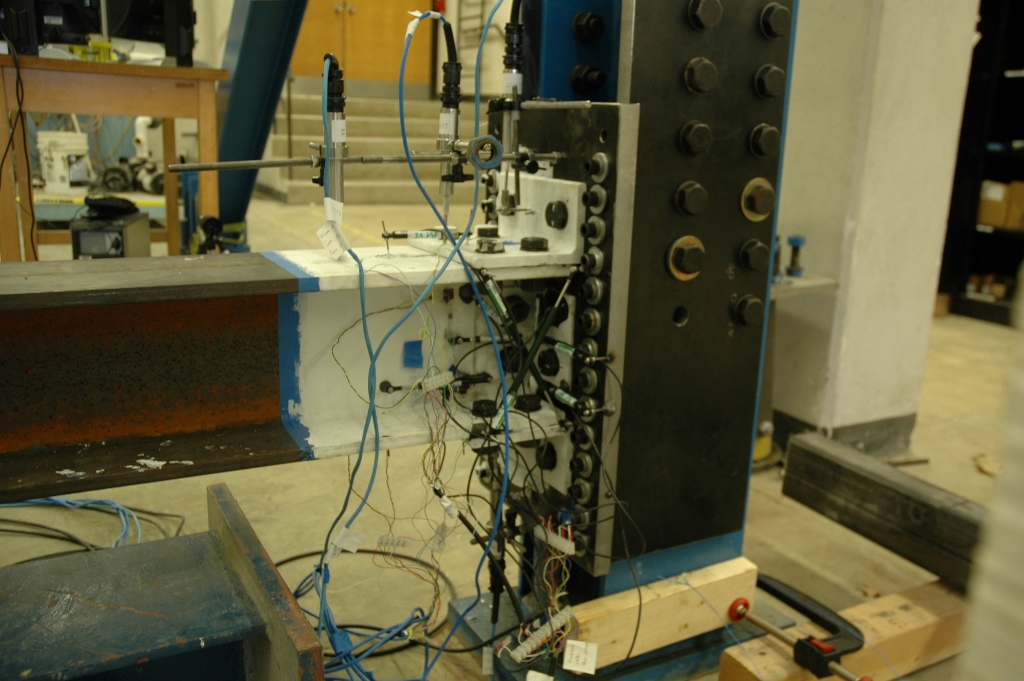
|