As Fracture Questions Remain, Team Raced to Save
Mississippi River Bridge
by Jim Parsons - August 30, 2021
A team of Michael Baker International, HNTB
and Kiewit scrambled to implement permanent
repairs for bridge linking Tennessee and
Arkansas
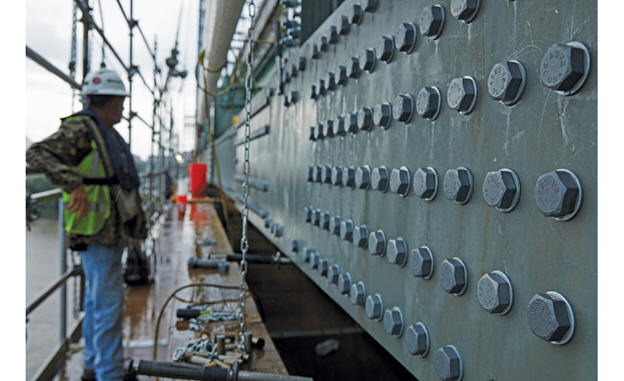
After scrambling during
the emergency, contractors were able to complete
permanent repairs in 83 days.
Photo courtesy Kiewit
"How is this bridge still
standing?”
That was the initial
reaction of Aaron Stover, Michael Baker
International’s vice president and regional
bridge practice lead, as he first studied images
of a fractured tie beam that forced the May 11
emergency shutdown of the I-40/Hernando de Soto
Bridge between Tennessee and Arkansas.
Discovered by chance earlier in the day during
MBI’s routine above-deck inspection, the
fracture on the bridge’s eastbound span affected
nearly half the cross-section of a 26-in. by
33-in. welded girder supporting one of the
50-year-old structure’s 900-ft-long, 100-ft-high
arched navigation spans across the Mississippi
River.
Though component
fractures are not unusual on older structures,
Frank Russo, MBI’s national bridge technical
director, says the de Soto Bridge crack was
nevertheless puzzling. The tie beam’s
1-3/8-in.-thick top flange plate and outer
½-in.-thick web plate were totally severed, with
the fracture extending across nearly half of the
bottom flange plate. Additionally, 9 ft of the
weld connecting the inside web with the upper
flange had separated as well.
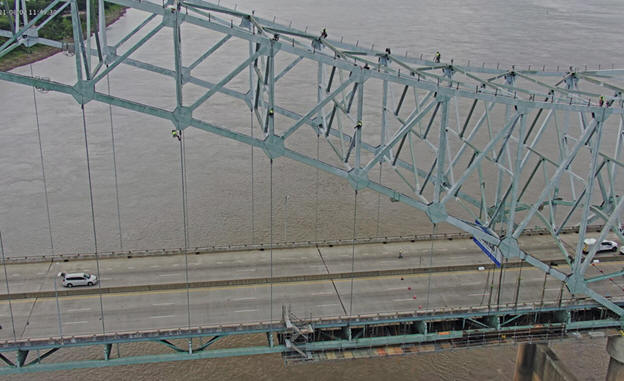
Shortly after the
fracture was discovered, the 900-ft-long bridge
spans were closed, and inspections began.
Photo courtesy Michael Baker International
“Usually when something
like this breaks, you find it completely
broken,” Russo says. “It’s very remarkable that
this member didn’t completely fracture.”
Though the fissure’s
cause and characteristics remain under
investigation, two things were clear as the
bridge was immediately closed to traffic—its
condition needed to be thoroughly assessed in
the event there was additional damage and a
repair strategy needed to be developed as
quickly as possible.
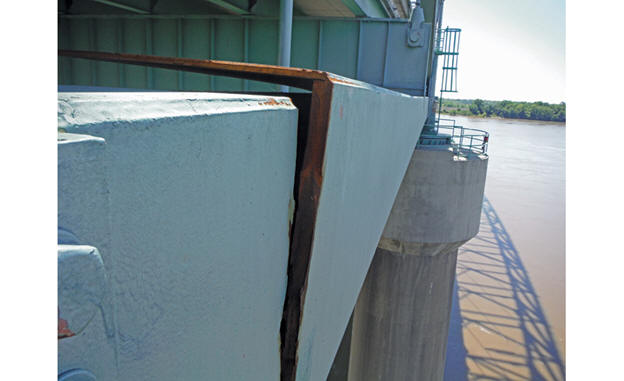
The fracture was
discovered by chance on May 11.
Photo courtesy Michael Baker International
Despite the fracture’s extraordinary
aspects, there is a strong familiarity among the
team tasked with carrying out the assessment,
both with the de Soto Bridge and each other. The
Arkansas and Tennessee transportation
departments have long shared responsibility for
the structure, with ARDOT overseeing inspection
and TDOT handling maintenance. MBI, which would
lead the response’s aerial inspection and design
work, had worked with both agencies, as had
HNTB, which performed a full hands-on inspection
of both tied-arch spans. Experts from the
Federal Highway Administration were also
involved.
The resulting bridge
section has a span of 72 meters (about 236
feet)—enough to span many rivers and highways.
Sections can also be daisy-chained and connected
into longer bridges. Each girder weighs over 50
tons, and they’re lowered carefully and
symmetrically over a pretty long time.
Traditionally constructed bridges are also often
built out symmetrically, because even small
imbalances can break the foundations that have
been constructed.
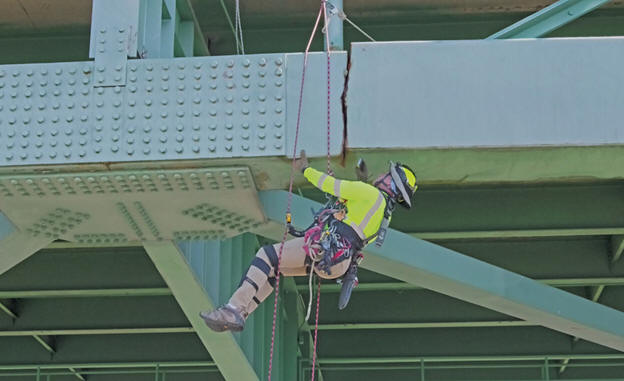
An inspector gets a
close-up view of the fracture.
Photo courtesy Michael Baker International
“It’s very
remarkable that this member didn’t completely
fracture.”
—Frank Russo, National Bridge Technical
Director, Michael Baker International
“That gave us a deep
bench of structural engineering expertise and
resources, allowing for a significant amount of
analysis and design to take place in a very
short amount of time and with a high level of
reliability and accuracy,” says ARDOT spokesman
Dave Parker.
The team also had
technology on its side, with drone video
combining with physical inspections using
rope-access techniques to expedite the condition
assessment. Drones also allowed the physical
inspection of the fracture to be streamed in
real time to the office-based design team.
“We could see what the
inspector was doing and ask to check out
additional aspects, which helped us start
planning multiple steps ahead,” says MBI bridge
technical director Jason Stith. “It was quite
incredible to get that information during a
two-hour conference call rather than having to
go back and forth over several days.”
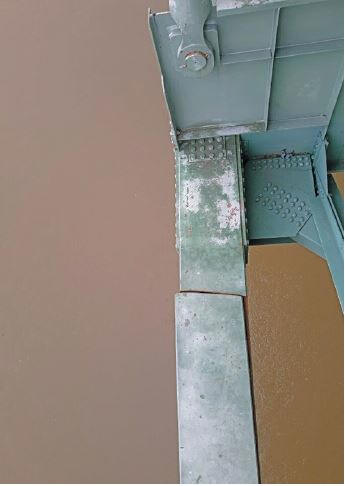
This image shows the view
when inspectors first discovered the crack.
Photo courtesy Tennessee Dept. of Transportation
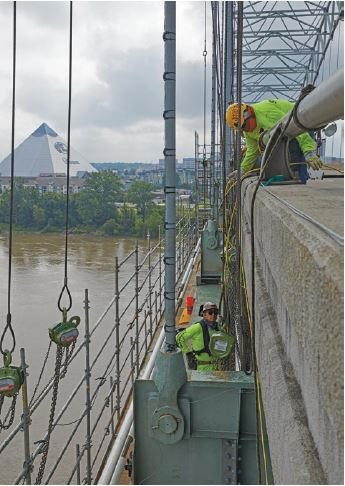
The emergency situation
for this vital connection between Tennessee and
Arkansas required work to progress on a 24/7
basis.
Photo courtesy Kiewit
Multi-path
planning
Though no additional
damage was found on the bridge, in-depth
inspections indicated that the structural load
at the fracture had been shed to the remaining
web and flange sections, putting those
components under exceptional stress.
“We needed to understand
that better before we started yanking around on
the bridge, trying to move things back to where
they were,” Stover says.
As the team began
concurrent design efforts to stabilize the
structure and devise a permanent repair, TDOT
implemented an emergency construction
manager/general contractor procurement that
agency commissioner Clay Bright says had the
capability “to get involved in the difficult,
challenging and at the time, still unknown final
repair design.”
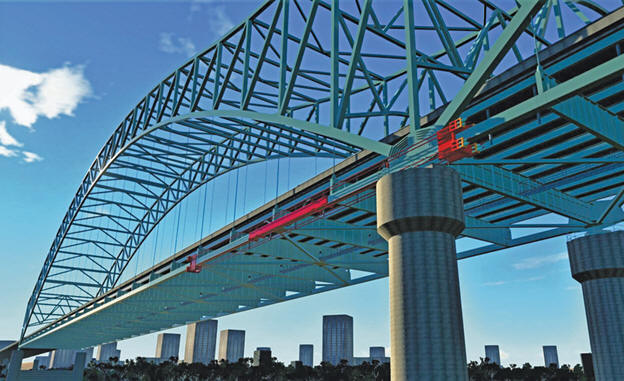
Sections highlighted in
red indicate the areas where repairs were
needed.
Rendering courtesy Michael Baker International
On the afternoon of May
17, less than two hours after TDOT had selected
Kiewit for the project, operations vice
president and area manager Chris Frieberg and
other firm representatives were discussing
stabilization and repair alternatives with the
design team.
“We worked through risks
associated with different design options and the
best way to mitigate them, as well as material
availability and fabrication lead time,”
Frieberg says. He adds that the solution had to
be one the design team could stand behind and
his team could build safely.
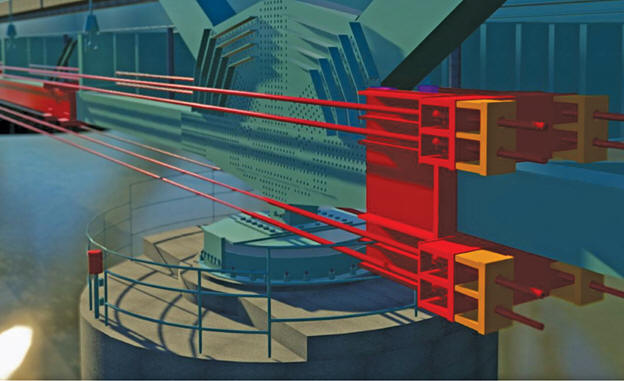
Rendering courtesy
Michael Baker International
“And it had to be
permanent, so that the DOTs would be assured of
having a safe structure for years to come,” he
adds.
The resulting two-phase
strategy called for first stabilizing the
fracture area with a “splint” of steel plating
that would add redundancy to structure. Because
the girder was slightly twisted and warped, the
plates would be offset to prevent placing any
new stress on the area.
While TDOT originally
envisioned basing the repair effort from barges,
the design team’s loading analysis indicated
that the fracture area could be safely accessed
from the bridge deck.
“That gave us a more
controlled environment for the delicate work we
were doing, although we did have to keep
personnel and equipment to a minimum,” Frieberg
says.
By the end of that first
week, Kiewit had assembled a 100-sq-ft suspended
platform to install the first of 30,000 lb of
HPS70W structural steel plates fabricated on an
expedited basis at Stupp Bridge Co. in Bowling
Green, Ky.
Over the next four and a
half days, crews used chain and air hoists to
lift the plates into place, where they were
secured with nearly 450 temporary bolts.
Frieberg says the work involved some lead paint
considerations and confined space protocols when
working inside the tie beam but required no
additional measures for COVID-19.
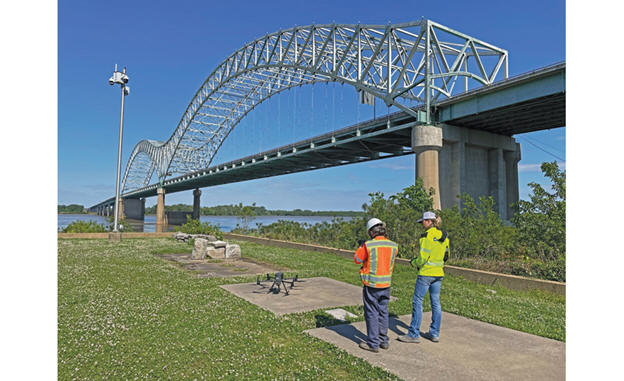
The ability to use drones
to inspect the damaged bridge aided the project
team.
From stopgap to
structurally sound
By May 25, two weeks
after discovery of the fracture, the de Soto
bridge was deemed sufficiently stabilized and
safe enough for TDOT to reopen the underlying
river channel to barge traffic and transition to
the next repair phase. A 150-ft-long section of
tie girder encompassing the fracture area would
be beefed up with 108,000 lb of additional
redundancy plating, with eight 3-in.-dia
high-strength post-tensioning rods installed
alongside the beam to transfer more than 1.2
million lb of tension to the composite section.
The supplemental
post-tensioning also allowed workers to remove
fractured flange sections for analysis.
“If the entire tie
decided to break, which is very unlikely, it has
a completely redundant element on the outside
that can carry the load,” Russo says.
Frieberg says this
strategy required an even higher level of
coordination and analysis given that the
precision fabrication of specialized
post-tensioning components and weldments and
additional strengthening plates had to be synced
with mobilizing specialty subcontractors and
addressing other logistics needs.
“We had three critical
paths running simultaneously, and the art of the
dance was keeping them all in unison,” he says.
“All three converged so that as the design was
signed and sealed, material fabrication was
underway.”
By July 3, the last of
the plates at the fracture location had been
bolted into place. But there was still one more
important step to complete before the bridge
could be declared fully restored. During the
initial condition inspection, HNTB conducted
non-destructive phased array ultrasonic testing
on the tie girders’ 500 welds to determine if
similar cracks were forming or could form under
certain conditions. Seventeen welds were found
to have anomalies, which Kiewit plated over the
next three weeks with a total of 78,000 lb of
steel to provide additional redundancy. Another
29 weld defects were ground or cored out.
“It had to be permanent
so that the DOTs would be assured of having a
safe structure for years to come.”
—Chris Frieberg, Operations Vice President,
Kiewit
After another round of
inspections, the de Soto Bridge’s eastbound
lanes were reopened to traffic on July 31,
followed two days later by the westbound lanes.
That completed an 83-day, 24/7 marathon that was
remarkably free of weather interruptions. Costs
for the routine and specialized inspections and
repairs, currently estimated at $10 million,
will be shared by both DOTs.
The effort also concluded
what ARDOT’s Parker considers to be a parallel
success story—safely shifting the de Soto
Bridge’s 40,000 vehicles per day to other
crossings, particularly the nearby 72-year-old
truss bridge that carries I-55 across the river.
Parker credits the team’s
collaborative brainstorming of congestion relief
strategies for helping cut the I-55 bridge’s
initial hour-long peak-hour backups by more than
half and reducing bail-out traffic onto local
roads. Both DOTs stepped up services to minimize
the effects of lane-closing incidents. TDOT’s
Bright notes that motorists’ initial concerns
about the safety of the I-55 bridge were
alleviated by emergency inspections and the
performance of the “robust structure” while the
de Soto Bridge was out of service.
“The only issue was a
pavement failure in one lane that was quickly
addressed during a weekend temporary lane
closure,” Bright says, adding that the bridge is
currently undergoing its scheduled biannual
inspection. “Any new issues will be addressed
along with other maintenance work next spring.
Meanwhile, the fractured
tie girder section is at Wiss Janney Elstner’s
forensic laboratory in Northbrook, Ill.,
undergoing metallurgic and other tests in an
effort to fully understand the factors that led
to the fracture. Parker says results of that
investigation, scheduled to be delivered by
fall, will help the DOTs determine if the
structure requires additional attention on top
of regularly scheduled inspections and
maintenance. A solar-powered strain gauge
monitoring system installed prior to the
bridge’s reopening also remains operational.
What’s already certain,
team members agree, is the essential role
team-wide collaboration played in turning a
potential catastrophe into a success story.
“If you listened into our
daily calls, you wouldn’t have been able to tell
who was DOT, who was designer and who was the
contractor,” Frieberg says. “Going through the
process, we were very well integrated and very
open-minded. That was the biggest contributor
with coming up with a design solution that could
be implemented quickly and safely.”
Questions Remain
in Inspection Oversight Controversy
Within hours of the
discovery of the de Soto Bridge tie girder,
images and video emerged suggesting that the
fissure had been months, perhaps even years in
the making despite having been unreported in at
least two ARDOT-led annual fracture-critical
inspections. Following an internal investigation
launched immediately after the closure, ARDOT
fired Monty Frazier, a 15-year employee who had
led the 2019 and 2020 de Soto Bridge
inspections. In addition, the Federal Highway
Administration launched an assessment and
compliance review of ARDOT’s bridge inspection
program, with the results expected by the end of
September.
Frazier’s reported
assertion that the mobile under-bridge
inspection platforms were unsafe to use was
countered by the agency’s heavy bridge
maintenance staff (HBMS), which, according to an
ARDOT interim after-action report, verified that
the equipment was stable and provided adequate
access to perform hands-on inspection at the
fracture location. Nine other fracture
structures inspected by Frazier were reexamined
and found to be safe.
Frazier has since
admitted that missing the fracture was a mistake
on his part, but he insists he’s not solely to
blame. In an interview with the Daily Memphian
newspaper, published on July 22, Frazier said he
pointed to the crack’s appearance in photos
reputedly dating as far back as 2014 as proof
that other inspectors overlooked the condition
as well. “If there are that many people who
missed the crack over all that time,” Frazier
told the reporter, “it’s a problem with the way
we inspect the bridge, not just the one guy who
happened to be on the paperwork the last time we
missed it.”
ARDOT has not verified
the validity of the photos and declined to
comment on the story. Meanwhile, multiple
investigations are underway, including an
agency-requested probe by the U.S. Dept. of
Transportation’s Office of Inspector General as
to whether Frazier’s alleged negligence
constitutes a criminal action. A parallel
internal investigation by ARDOT’s human
resources department is proceeding as well.
In July, ARDOT boosted
its historic bridge maintenance system budget by
nearly $3 million, providing funding for
consultants that will help the agency identify
new technologies, improve quality assurance and
quality control and improve inspector training.
|