Part 6.
Concrete Aggregates
Aggregates generally occupy 70 to 80% of the volume of concrete and therefore have a
significant effect on its properties. Strength of concrete and mix design are independent
of the composition of aggregate, but durability may be affected. Aggregates are classified
based on specific gravity as heavyweight, normal-weight, and lightweight. Normal weight
aggregates make-up 90% of concrete used in the United States.
Shape and Texture
Shape and texture affect workability of fresh concrete. The ideal aggregate would be
spherical and smooth allowing good mixing and decreasing interaction between particles.
Natural sands are close to this shape. However, crushed stone is much more angular and
requires more paste to coat the increased surface area. Long, flat aggregate should be
avoided due to increased interaction with other particles and the tendency toward
segregation during handling.
Shape and texture of coarse aggregates affects the strength of the concrete mix.
Increased surface area provides more opportunity for bonding and increases strength.
However, excessive surface area in an aggregate can lead to internal stress concentrations
and potential bond failure.
Size Gradation
Grading or aggregate size distribution is a major characteristic in concrete mix
design. Cement is the most expensive material in concrete. Therefore, by minimizing the
amount of cement, the cost of concrete can be reduced.
- Sieve
Analysis -- determines the grading of an aggregate. Coarse aggregate is that
retained on the #4 sieve and fine aggregate is that passing a #4 sieve. In a sieve
analysis a series of sieve are used with smaller and smaller openings. Coarse aggregates
are analyzed with standard sieves and fine aggregates with half-sized sieves.
- Maximum
Aggregate Size -- Smallest sieve in which the entire sample will pass through.
The maximum nominal size is the smallest sieve in which at least 95%, by weight, of the
sample will pass. Maximum size should not be larger than 1/5 the minimum dimension of a
structural member, 1/3 the thickness of a slab, or 3/4 the clearance between reinforcing
rods and forms. These restrictions limit maximum aggregate size to 1 1/2 inches, except in
mass applications.
Higher maximum aggregate size lowers paste requirements, increases strength and reduces
w/c ratios. However, excessively large aggregate tends to lower strength by
reducing available bonding area. ASTM has limits for grading of concrete aggregates.
- Fineness
Modulus -- a parameter for checking the uniformity of grading. Generally
calculated for fine aggregates but also for coarse aggregates assuming 100% is retained on
#8 - #100 sieves. Therefore, for fine and coarse aggregates respectively, the fineness
modulus is:
F.M. = (Cumulative percent retained on half-sized sieves)/100
F.M. = (Cumulative percent retained on standard sieves including #4 +
500 )/ 100
A fineness modulus for fine aggregates should be 2.3 - 3.1. Two aggregates with the
same fineness modulus can have different grading curves. A low fineness modulus requires
more cement paste to maintain workability. Variations from mix design requirements for
fineness modulus should not exceed 0.2 (ASTM standards). ASTM allows for an increase in
fine aggregates (% passing #50 and #100) if smoother surface finishing is required.
However, there are solid restrictions on very fine particles to prevent increased water
demand and volume instability.
Gap Grading -- An aggregate where one or more of the intermediate-sized fractions is
omitted. Advantages of gap grading are more economical concrete, use of less cement, and
lower w/c ratios. The resulting concrete is very stiff and has low
workability. An extreme case is no-fines concrete. This concrete is difficult to handle
and compact; developing low strength and high permeability.
Moisture Content
Aggregate can contain water, both internal, based on porosity, and external, surface
moisture. This gives aggregate the ability to absorb water. This will effectively reduce
the amount of water available for hydration; or conversely, if the aggregate is very wet,
add excess water to a cement mix.
There are four moisture states:
- Oven-dry (OD); all moisture removed.
- Air-dry (AD); surface moisture removed, internal pores partially full
- Saturated-surface-dry (SSD); surface moisture removed, all internal
pores full.
- Wet; pores full with surface film.
Of these four states, SSD, saturated-surface-dry, is considered the best reference
state. It is an equilibrium state, where the aggregate will not absorb or give water to
the cement paste, simulates actual field conditions more closely, and used to determine
bulk specific gravity. However, this moisture state is not easy to obtain.
Absorption and Surface
Moisture
To determine the amount of water an aggregate will add or subtract from a cement paste,
the following three quantities are used:
- Absorption capacity (AC) -- maximum amount of water the
aggregate will absorb. The range for most normal-weight aggregates is 1 - 2%.
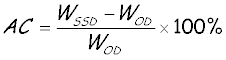
- Effective Absorption (EA) -- amount of water required to bring
an aggregate from the AD state to the SSD state.
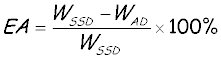
The weight of water absorbed by the aggregate Wabs
is calculated from the weigh of the aggregate Wagg
in a concrete mix using effective absorption (EA).
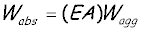
- Surface Moisture (SM) -- amount of water in excess of SSD
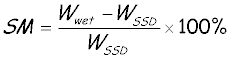
It is used to calculate the additional water Wadd
of the concrete mix
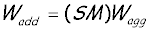
The moisture content (MC) of aggregate is given by:
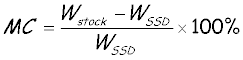
If the moisture content (MC) is positive, there is surface
moisture. If the MC is negative, it has the potential for
absorption. Therefore, the total moisture associated with an aggregate is:
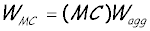
Stockpiled fine aggregate is often in a wet state with a surface moisture of 0 to 5%.
More water can be held in the interspace between particles than in coarse aggregates. This
also leads to thicker films of water which in turn push the aggregate apart and increase
the apparent volume. This is called bulking.
Specific Gravity
A dimensionless ratio of density of the material in question to the density of water.
SG = [density of solid] / [density of water]
Absolute specific gravity (ASG) considers the weight and volume of the solid part of
the aggregate. Whereas, bulk specific gravity (BSG) is a measure of the weight/volume of
solids and pores of a material.
ASG > BSGSSD > BSGOD
However, since the porosity of most rocks used in concrete is 1 to 2%, the values of
all specific gravities are approximately the same; in the range of 2.5 to 2.8.
Unit Weight
Unit weight (UW) or bulk density is the weight of a given volume of material.
Basically, unit weight is measured by filling a container of known volume with a material
and weighing it. The degree of moisture and compaction will affect the unit weight
measurement. Therefore, ASTM has set a standard oven-dry moisture content and a rodding
method for compaction. The maximum unit weight of a blend of two aggregates is about 40%
fine aggregate by weight. Therefore, this is the most economical concrete aggregate since
it will require the least amount of cement.
Durability of Aggregates
Aggregates makeup the largest part of concrete mixes and are responsible for the
durability of the mix. Durability is a measure of how well concrete will handle freezing
and thawing, wetting and drying, and physical wear. Chemical reactions also can contribute
to problems with durability.
- Soundness
-- rocks that undergo volume changes due to wetting and drying are rare. However,
aggregate is susceptible to volume change during freezing and thawing cycles. Freezing can
cause internal stresses to build up as water inside the aggregate freezes and expands. A
critical size can be calculated below which freeze-thaw stress is not a problem; however,
for most rock it is greater than normal sizes.
- Wear
Resistance -- a good aggregate will be hard, dense, strong, and free of porous
material. The abrasion resistance of aggregate can be tested by the Los Angeles abrasion
test; however, this test does not match well with concrete wear in the field.
- Alkali-Aggregate
Reaction -- An expansive reaction between some reactive forms of silica with the
aggregate and alkalis in the cement paste. The result is overall cracking in the
structure, manifesting itself in map or pattern cracking at the surface. This reaction can
be controlled most easily by using low-alkali cements. However, due to changes in
manufacturing, low-alkali cements may not be feasible. A better approach is to avoid
aggregate with the potential or proven record of reactivity. A low w/c ratio is
very impermeable and will slow down the reaction but not stop it. No adverse reactions
will occur without external water.
- Other
Alkali-Silica Reactions -- sand-gravels found in river systems of Kansas and
Nebraska are highly reactive and cause map cracking. Replacement of 30% of the aggregate
with crushed limestone is effective in reducing the damage. Basically, it results in the
separation of flat clay minerals causing very slow expansion.
- Alkali-Carbonate
Reactions -- an expansive reaction involving clayey carbonate rock. Reaction can
be controlled by using low-alkali cements or blending aggregate with other less reactive
material. ASTM has set standards for deleterious substances in aggregates, which depend on
application. This can be divided into two categories:
Impurities
Solid
materials - particles passing a 200-mesh sieve. These fine particles may increase
water requirements and interfere with surface bonding between cement and coarse
aggregates.
Soluble
substances - organic matter may interfere chemically with alkaline cement pastes
affecting setting time. Aggregates obtained from the sea should be thoroughly cleaned to
avoid problems from salt contamination.
Unsound
particles -- Soft particles such as clay lumps, wood, and coal will cause pitting
and scaling at the surface. Organic compounds can be released which interfere with setting
and hardening. Weak material of low density which have low wear resistance should also be
avoided.
Evaluation of Aggregates
It should be noted that tests on aggregates alone are not an effective means of
predicting aggregate performance in the field. Tests for aggregate properties for mix
design are straightforward. However, tests for durability and performance have
limitations.
Physical Tests
- Abrasion
Resistance
- Abrasion
resistance -- The Los Angeles test for abrasion involves ball milling an
aggregate sample for a given time and measuring how the sample particles are reduced in
size.
- Scratch
hardness test -- assumes a relationship between hardness and abrasion.
Neither of this tests are an accurate or reliable measure of the concrete hardness. An
indication would be to test the concrete itself.
- Frost
Resistance
- Soundness
test -- This test is a simulation of ice formation in an aggregate sample. The
sample is saturated with a solution of sodium or magnesium salt and dried in an oven. The
salt crystals which form in the pores simulate ice. Correlation between this test and
field tests are not good. Again, a better approach is testing aggregate in concrete.
Chemical Tests
- Alkali-silica
Reaction -- A rapid reliable test for alkali-aggregate reactivity has not yet been
developed. Most acceptable tests require long curing times of about 6 months. In this
test, the aggregate is ground into a fine sand and used to make a variety of mortar bars.
The mortars are stored in hot, moist conditions to accelerate the reaction. Expansion of
the sample is measured and compared to ASTM specifications.
- Aggregate
Beneficiation -- If an aggregate does not pass the ASTM tests, an engineer may choose to
try to upgrade the material. Beneficiation may be useful in areas where aggregate is
scarce. There are several possible ways of treatment:
- Crushing
-- Soft, porous rock may be removed by crushing.
- Heavy-media
separation -- Lightweight particles may be separated by floating them to the top
of a liquid.
- Reverse water
flow or air flow -- used to remove lightweight particles like wood.
- Hydraulic
jigging -- Stratification of aggregate in a vertical pulsation of water.
Lightweight particles separate to the top.
- Elastic
fractionation -- Aggregate is dropped on an incline steel plate. Hard particles
bounce higher off the plate than do softer particles. Appropriate placement of collection
bins can provide good separation.
- Washing and
scrubbing -- Removes fine surface particles.
Waste Materials as
Aggregate
The use of waste materials as aggregate in concrete is gaining increased attention,
especially in view of our escalating solid-waste problems. A wide variety of materials are
being considered as aggregates: garbage, building rubble, industrial waste products, and
mine tailings. All of these potential aggregates are evaluated on their 1) economy, 2)
compatibility with other materials, and 3) concrete properties. Successful utilization of
waste material as aggregate depends on anticipating potential problems and ensuring that
the properties of concrete will remain unchanged.
Special Aggregates
Aggregates are classified by their specific gravities into three categories; 1)
lightweight, 2) normal-weight, 3) heavy-weight; each with different applications.
- Lightweight
Aggregates -- A general characteristic of lightweight aggregate is high internal
porosity. Most of these materials are synthetic, however, some natural materials can be
treated to provide low specific gravity. Clays, shale, or slates will bloat at high
temperatures resulting in an expansion in volume. Other synthetic materials are produced
using pyroprocessing techniques, such as volcanic glass, slags, or waste glass.
Lightweight aggregates have high absorption capacity associated with their high porosity.
However, some materials have a coating resulting from the fusion process and water cannot
penetrate. This coating can be damaged during handling resulting in an abrupt increase in
absorption.
- Heavyweight
Aggregates -- A material with a high specific gravity. These types of materials
are mostly used for radiation shielding and application where a high mass-to-volume ratio
is required.
- Abrasion and
Skid-Resistant Aggregates -- Hard, dense aggregates used in heavy-industry
applications where high resistance to abrasion is required. The strength of the cement
paste and the cement-aggregate bond are more important than the aggregate hardness.
- Marginal
Aggregates -- Use of this type of aggregate will require more care and thought in
design, and generally more cost. In considering marginal aggregates, there are four areas
of interest: 1) concrete properties, 2) weaknesses of aggregate, 3) beneficiation, and 4)
use of protective measures.
This website was originally developed by
Charles Camp for his
CIVL 1101 class.
This
site is maintained by the
Department of Civil
Engineering at the
University of Memphis.
Your
comments and questions are more than welcome.
|